精确控制:伺服驱动模块能够提供高度精确的运动和位置控制。它们通常能够实时监测和调整电机的速度、位置和力矩。高性能:这些模块通常具有高性能的处理器和控制算法,以实现快速响应和高精度的运动控制。反馈系统:伺服驱动模块通常配备了反馈系统,如编码器或传感器,以实时获取电机的位置和速度信息,从而实现闭环控制。多种通信接口:它们通常支持多种通信接口,如以太网、Modbus、CAN等,以便与其他设备和系统集成。保护功能:伺服驱动模块通常具有过流、过热、过压和欠压等保护功能,以确保电机和设备的安全运行。多轴控制:一些伺服驱动模块支持多轴控制,可以同时控制多个伺服电机。
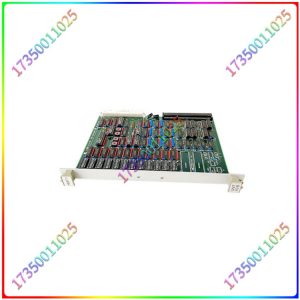
VME-U10B
由于转子和定子加热和冷却集成在一个模型中,因此使用较长的冷却时间常数转子或定子。但是,如果没有提供冷却时间常数,则必须确定设置。在确定冷却时间常数设置之前,应考虑电机的占空比。如果电机通常在没有过载负荷要求的情况下启动并连绫运行很长时间,则冷却时间常数可能很大。这将使热模型变得保守。如果电机的正常占空比涉及频繁启动和停止,且具有周期性过载占空比要求,则冷却时间常数需要更短,更接近电机的实际热极限。
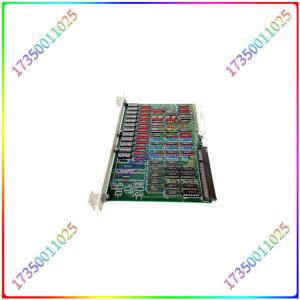
VME-U10B
通常情况下,电机在启动过程中受到转子限制。因此,定子中的RTD不能提供确定冷却时间的佳方法。运行和停止冷却时间常数的合理设置的确定可以按优先顺序列出的以下方式之一完成。电机运行和停止冷却时间或常数可在电机数据表上提供,或由制造商提供。编程灵活性:它们通常具有编程灵活性,允许工程师根据特定的应用需求编写自定义控制代码。
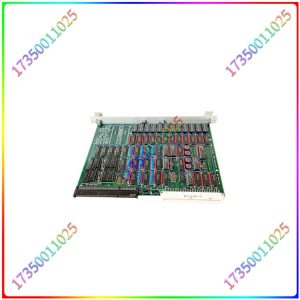
VME-U10B
Precise control: The servo drive module can provide highly accurate motion and position control. They are usually able to monitor and adjust the speed, position, and torque of the motor in real-time. High performance: These modules typically have high-performance processors and control algorithms to achieve fast response and high-precision motion control. Feedback system: The servo drive module is usually equipped with a feedback system, such as an encoder or sensor, to obtain real-time position and speed information of the motor, thus achieving closed-loop control. Multiple communication interfaces: They typically support multiple communication interfaces, such as Ethernet, Modbus, CAN, etc., for integration with other devices and systems. Protection function: The servo drive module usually has protection functions such as overcurrent, overheating, overvoltage, and undervoltage to ensure the safe operation of the motor and equipment. Multi axis control: Some servo drive modules support multi axis control and can simultaneously control multiple servo motors.
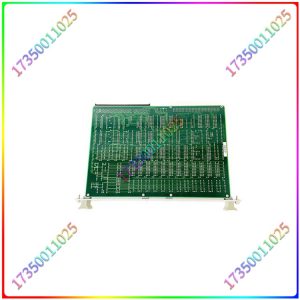
VME-U10B
Due to the integration of rotor and stator heating and cooling in one model, a longer cooling time constant is used for the rotor or stator. However, if a cooling time constant is not provided, the setting must be determined. Before determining the cooling time constant setting, the duty cycle of the motor should be considered. If the motor is usually started without overload requirements and runs continuously for a long time, the cooling time constant may be large. This will make the thermal model conservative. If the normal duty cycle of the motor involves frequent starting and stopping, and has periodic overload duty cycle requirements, the cooling time constant needs to be shorter and closer to the actual thermal limit of the motor.
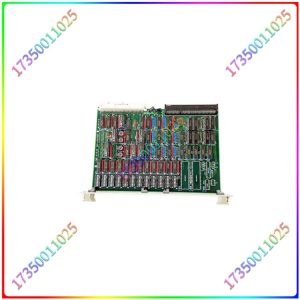
VME-U10B
Usually, the motor is limited by the rotor during startup. Therefore, the RTD in the stator cannot provide a good method for determining the cooling time. The determination of the reasonable setting of the running and stopping cooling time constants can be achieved by one of the following methods listed in priority order. The running and stopping cooling time or constants of the motor can be provided on the motor data sheet or by the manufacturer. Programming flexibility: They typically have programming flexibility, allowing engineers to write custom control code based on specific application requirements.
There are no reviews yet.