伺服电动机伺服电动机有两项技术值得注意,一是高密度电机, 采用-种叫“大极电机”的设计思想。例如六极九槽电机,定子由九个独立的极构成,在每个极上绕制集中线圈,然后再将九个极拼装起来,形成九个槽的电机铁芯。由于每个极是独立绕制和整形,所以即使采用自动机绕,也能保持槽满率高达90%。这类电机制造工艺好,空间利用和体积都达到了最小化,故称为高密度电机。从运行原理上讲,这类电机不属于旋转磁场电机,它在三相脉振磁场下工作,因此,它的适用性、设计方法和运行方式都有一定特殊性, 所以这类电机不适合方波电流驱动。另- 类是嵌入式磁钢速率伺服电动机,它可利用凸极效应引起的交、直轴电感随位置变化的特点,构成真正意义上的无位置传感器速率伺服电动驱动系统。传感器除了各类光电编码器以外,磁编码器值得关注。磁编码器的体积和重量都比光电编码器小几十倍,温度范围更宽,几乎不怕冲击和振动。其工作原理非常简单,它的定子是一颗内嵌霍尔磁敏元件和DSP的芯片,体积可以小到MSOP-24封装,它的转子是一颗两极磁钢。 它的分辨率10- -12位, 精度8- -10位。 这种磁编码器已有供应。作为空间应用, 为了满足-35°C- -80°C环境要求, 几乎难以采用传统的光电编码器,为此我们自行研制了磁编码器,分辨率16位,精度12位。磁编码器信号处理电路共存于驱动控制电路(FPGA) 中,形成传感器与驱动控制电路一体化。
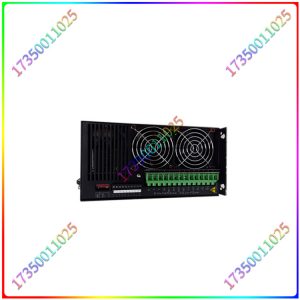
IC800SSI228RD2-CE
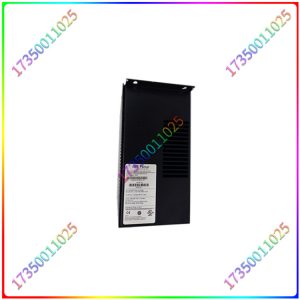
IC800SSI228RD2-CE
There are two noteworthy technologies for servo motors. One is high-density motors, which adopt a design concept called “large pole motors”. For example, in a six pole nine slot motor, the stator is composed of nine independent poles, with a concentrated coil wound on each pole, and then the nine poles are assembled to form a nine slot motor core. Due to the independent winding and shaping of each pole, even with automatic winding, the slot filling rate can be maintained up to 90%. This type of motor has a good manufacturing process, minimizes space utilization and volume, hence it is called a high-density motor. In terms of operating principle, this type of motor does not belong to a rotating magnetic field motor. It operates under a three-phase pulsating magnetic field. Therefore, its applicability, design method, and operating mode all have certain particularity, so this type of motor is not suitable for square wave current drive. Another type is an embedded magnetic steel rate servo motor, which can utilize the characteristics of the AC and DC axis inductance changing with position caused by the saliency effect to form a true position sensorless rate servo electric drive system. In addition to various types of photoelectric encoders, magnetic encoders are worth paying attention to. The volume and weight of magnetic encoders are dozens of times smaller than those of optical encoders, with a wider temperature range and almost no fear of impact and vibration. Its working principle is very simple. Its stator is a chip embedded with Hall magnetic sensors and DSP, and its volume can be as small as MSOP-24 packaging. Its rotor is a bipolar magnetic steel. It has a resolution of 10-12 bits and an accuracy of 8-10 bits. This type of magnetic encoder is already available. As a space application, in order to meet the environmental requirements of -35 ° C-80 ° C, it is almost difficult to use traditional photoelectric encoders. Therefore, we have developed our own magnetic encoder with a resolution of 16 bits and an accuracy of 12 bits. The signal processing circuit of the magnetic encoder coexists in the drive control circuit (FPGA), forming an integrated sensor and drive control circuit.
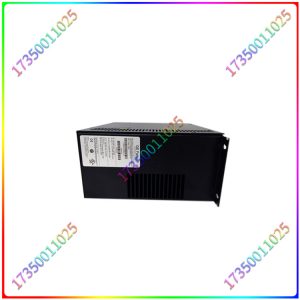
IC800SSI228RD2-CE
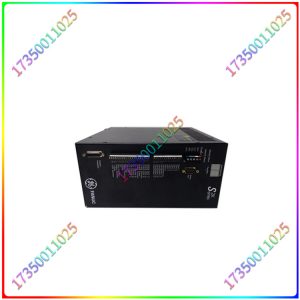
IC800SSI228RD2-CE
There are no reviews yet.